Pick and place robots do exactly what it says on the tin: pick things up from one location, such as a conveyor belt, and place them down in another, for example, on a pallet. The automated machines can be programmed to perform precise movements and can handle objects of all sizes with much greater speed, accuracy and consistency than a human operative.
This makes them a popular choice for manufacturers looking to increase efficiency and productivity.
Types of pick and place robots
There are four types of pick and place machines and each comes equipped with a different type of end gripper, to handle objects ranging from boxes to bottles:
1. Cartesian Robots
- Also known as gantry robots, these systems have a gantry or structural beams and work on three or four axes (X, Y, Z and a 4th rotation axis on the gripper head) to position items.
- They are capable of handling heavy loads and precise movements but output can be slow.
- Cartesian robots are commonly used for palletising and de-palletising goods, where they can be used to form complex pallet patterns, as well as in assembly and packaging processes.
2. Robotic Arm
- These are the simplest and most common type of pick and place robot.
- They usually work on six axes, although a palletiser only needs four axis, to perform palletisation.
3. Delta Robots
- Delta robots are ceiling-mounted and operate on three axes like the Cartesian models.
- They excel in high-speed operations and are often used for pick and place tasks in the food and beverage industry, including packaging and sorting applications.
- Delta robots are ideal for handling small and lightweight objects as they offer excellent speed and accuracy.
4. SCARA Robots
- SCARA (Selective Compliance Assembly Robot Arm) robots have a horizontal arm design with rotary joints – similar to a human arm with shoulder and elbow joints.
- They provide fast and precise vertical and horizontal movements, making them suitable for assembly, material handling, and sorting tasks.
- SCARA robots are frequently used in industries such as electronics, automotive, and consumer goods.
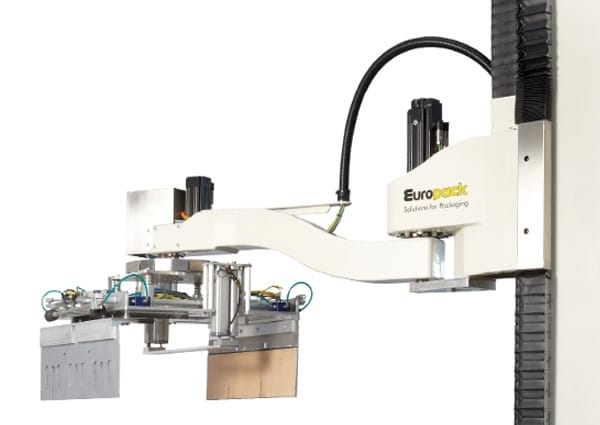
Reasons to install a pick and place robot
Incorporating pick and place robots, such as gantry palletisers, into your manufacturing operations can provide a significant boost to your business growth. Advantages include:
- Increased efficiency
The risk of human error is removed, and processes are faster. Pick and place robots can work 24/7 without the need for breaks or time off so production time is maximised. - Improved accuracy
Objects are placed accurately and consistently, every time, resulting in higher product quality, reduced waste and improved customer satisfaction. - Enhanced workplace safety
Automating repetitive and physically demanding tasks helps to reduce the risk of injuries and accidents in the workplace, creating a safer environment for workers. - Greater flexibility
Pick and place robots have different gripper heads to handle a range of packages, allowing new products to be introduced to a production line with minimal disruption and downtime. - Long-term savings
Although there are capital investment costs, the improvements in productivity, reduced downtime and less wastage mean manufacturers can soon see a return on investment.
A valuable asset
For manufacturers trying to work more efficiently, pick and place robots offer an effective solution. By automating repetitive and labour-intensive tasks, businesses can streamline their processes and stay ahead of the competition.
To find out how pick and place robots can benefit your operation, contact us for free advice.