As we’re poised to enter a new year, so the world of industrial automation in manufacturing is entering a new chapter.
New automation trends and technological advancements are reshaping the way businesses operate, with Artificial Intelligence (AI) and automation at the forefront of the transformation. In this blog, we’ll explore what the increasing use of AI means for manufacturers and how it can help them stay agile and efficient in a competitive market, as well as look at which other trends we can expect to see in 2025.
Artificial Intelligence (AI)
By far the most significant development expected is the continued adoption of AI and machine learning in a manufacturing setting. As we’ve seen in other industries, AI enables systems to analyse, learn and even make decisions autonomously, driving greater efficiency and quality control in a number of ways:
- Data-driven decision-making and machine learning
By analysing data from multiple sources, AI systems can identify inefficiencies and patterns and optimise production processes. Real-time data can be used to make small adjustments to improve efficiency and productivity, while long-term data trends guide strategic planning, enhancing areas such as supply chain management and demand forecasting.
- Predictive maintenance
The data can also be used to monitor equipment condition and detect the signs of wear or failure and the need for maintenance. This means manufacturers can schedule repairs proactively, reducing costly downtime and improving reliability, productivity and equipment life.
- Adaptive controls
AI-powered machines monitor their surroundings in real-time, adjusting to environmental changes, material variations or unexpected disruptions without compromising quality. This dynamic responsiveness ensures consistent output, even under rapidly changing demands.
Intelligent automation and hyperautomation
We’ve got used to introducing Robotic Process Automation (RPA) into manufacturing operations, which is the automation of repetitive rule-based tasks, such as sack-filling or palletising. However, it’s unable to manage more complex tasks, and this is where we expect to see a rise in the use of intelligent automation. Intelligent automation integrates AI, RPA and machine learning, allowing businesses to introduce more diverse, complicated processes and automate interconnected tasks. This more holistic approach generates new levels of productivity and flexibility in readiness for future growth.
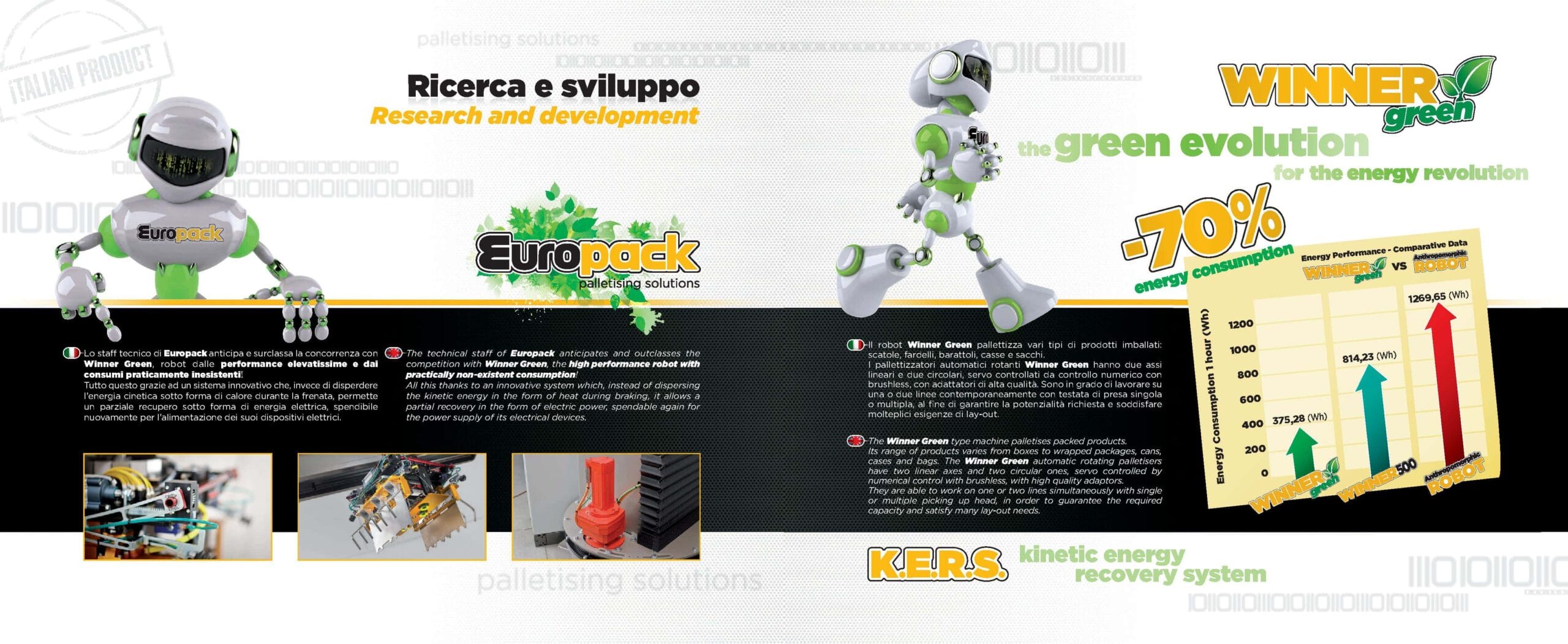
Energy efficiency and sustainable innovation
Sustainability is becoming a core driver of innovation in manufacturing processes and stricter carbon reduction targets are likely to bring increased pressure to reduce environmental impact. Equipment such as Europack’s Winner Green range of palletisers already uses the Kinetic Energy Recovery System (KERS) to reduce energy consumption by up to 70%, and we’re predicting further advances in technology that will reduce both environmental impact and operational costs. Manufacturers will also focus on how automation can improve resource efficiency and waste reduction (such as excess packaging) throughout production processes.
Co-creation and collaboration
Co-creation and collaboration with partners, customers and industry experts will be key drivers of innovation in industrial automation, especially as technology continues to develop and change apace. Involving specialists with particular insights and expertise allows for the creation of bespoke equipment and the implementation of new processes, which are in tune with the latest market developments and customer demands.
Industrial automation is changing. Automation has always been a driver of efficiency and growth but these trends are shaping a new future of manufacturing – a future which involves intelligent, hyper-automated systems that give manufacturers more opportunities to boost productivity and gain a competitive advantage.