PALpack were recently contacted by a global organisation via our website who were looking for an end of line palletising solution. Faced with space limitations, multiple product variations and two pallet sizes, various design and logistical challenges arose that made it difficult to find a supplier with the experience and knowledge to offer verifiable solutions to these challenges and design a single, reliable turn-key robot palletising cell.
Other packaging machine specialists had been contacted prior to PALpack, but using our knowledge and experience in bespoke conveying, wrapping and palletisation, we were able to overcome all these challenges, as well as any previously unforeseen by the client, to quickly fulfil the design brief, meet the required output levels and ultimately exceed expectations.
Key challenges
- Available space
- Existing line speeds
- Multiple product variations – two existing lines, each feeding a different pack size, at 350 p/h each (700 p/h total), with two pallets being stacked automatically working out lane priority
- Two pallet sizes requiring automated de-stacking. (1.2m x 1m &1.2m x 0.8m)
- Two different layer card sizes requiring automated positioning
- Efficient use of space to be able to integrate a fully automatic pallet stretch wrapper in addition to the two pallet de-stackers
- Requirement for operator to safely access all four corners of the pallet to manually position corner posts prior to stretch wrapping
Solutions
Available space
With 30 years’ experience in providing reliable end of line automation, we were able to bring to the table:
- Extensive and diverse design capability
- Extensive knowledge of available industry proven solutions
- Determination in producing over 20 different schematics until a working model could be achieved within the space allocated
- Utilisation of chain transfers and/or turntables to reorientate pallets prior to stretch wrapping
- Design and manufacture of compact automated pallet de-stackers
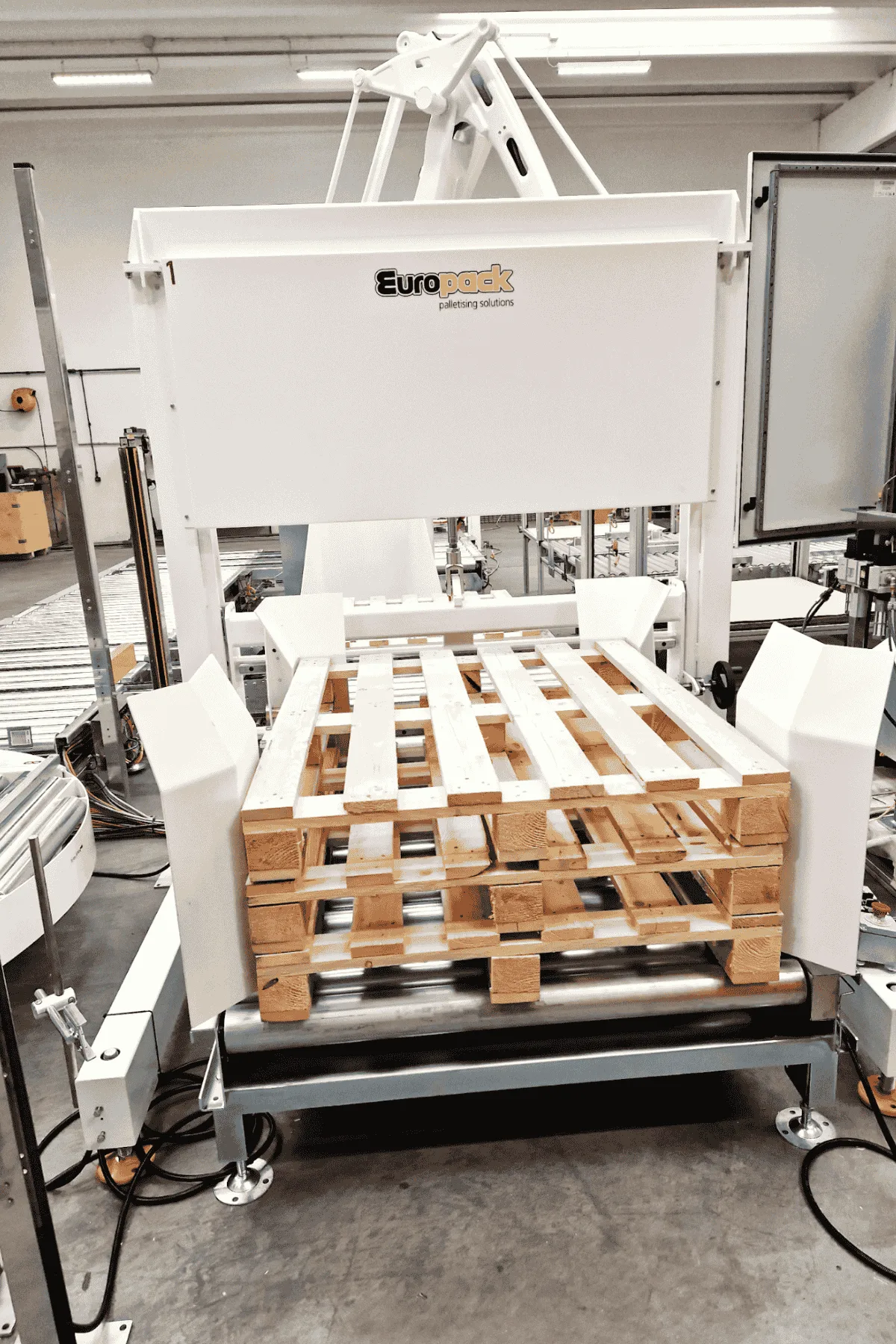
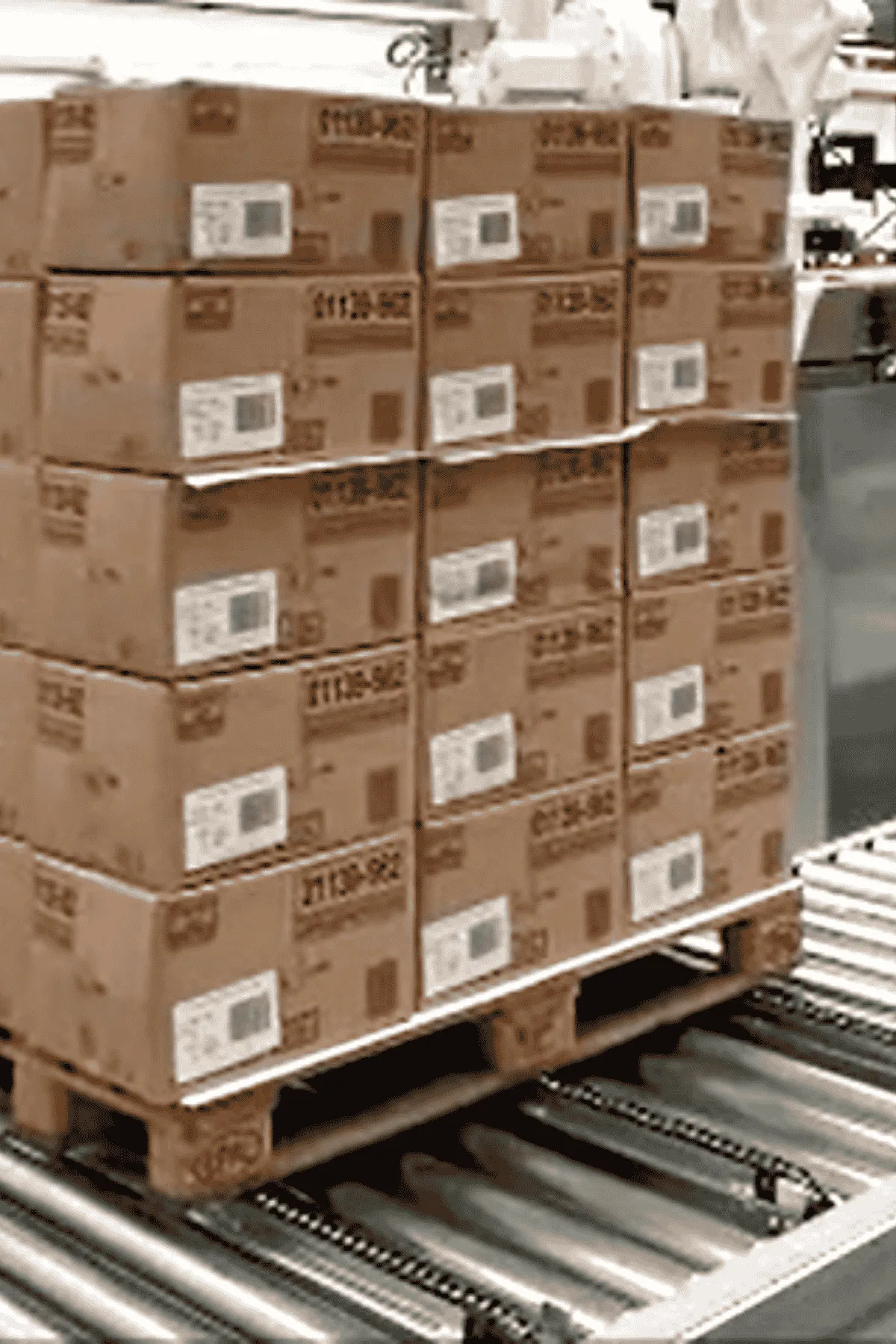
Our experience and knowledge allowed us to design a bespoke, positive mechanical paddle gripper that holds the packs without slippage or damage facilitating:
- Maximised robot speed by handling one pack at a time therefore reducing weight and concentrating grip area
- Ability to cope with slight deviations in pack sizes (if handling two or more packs, the gripper will grip the largest, causing the smallest to slip), this may result in slower speeds to compensate
- Overcoming inertia overrun by single pack handling and minimising pack weight
- Inertia overrun results in stopping the robot due to tripping out the servo drives stopping the cell
- The opportunity to demonstrate that positive single pack handling at high speed can generate a higher output than multiple pack handling
- Versatility in stacking patterns due to single pack handling, and 270-degrees rotation of gripper
- Maximum speeds attained due to single, positive pack gripping
- Central pack stabilising pad ensured pack is placed squarely on the pallet
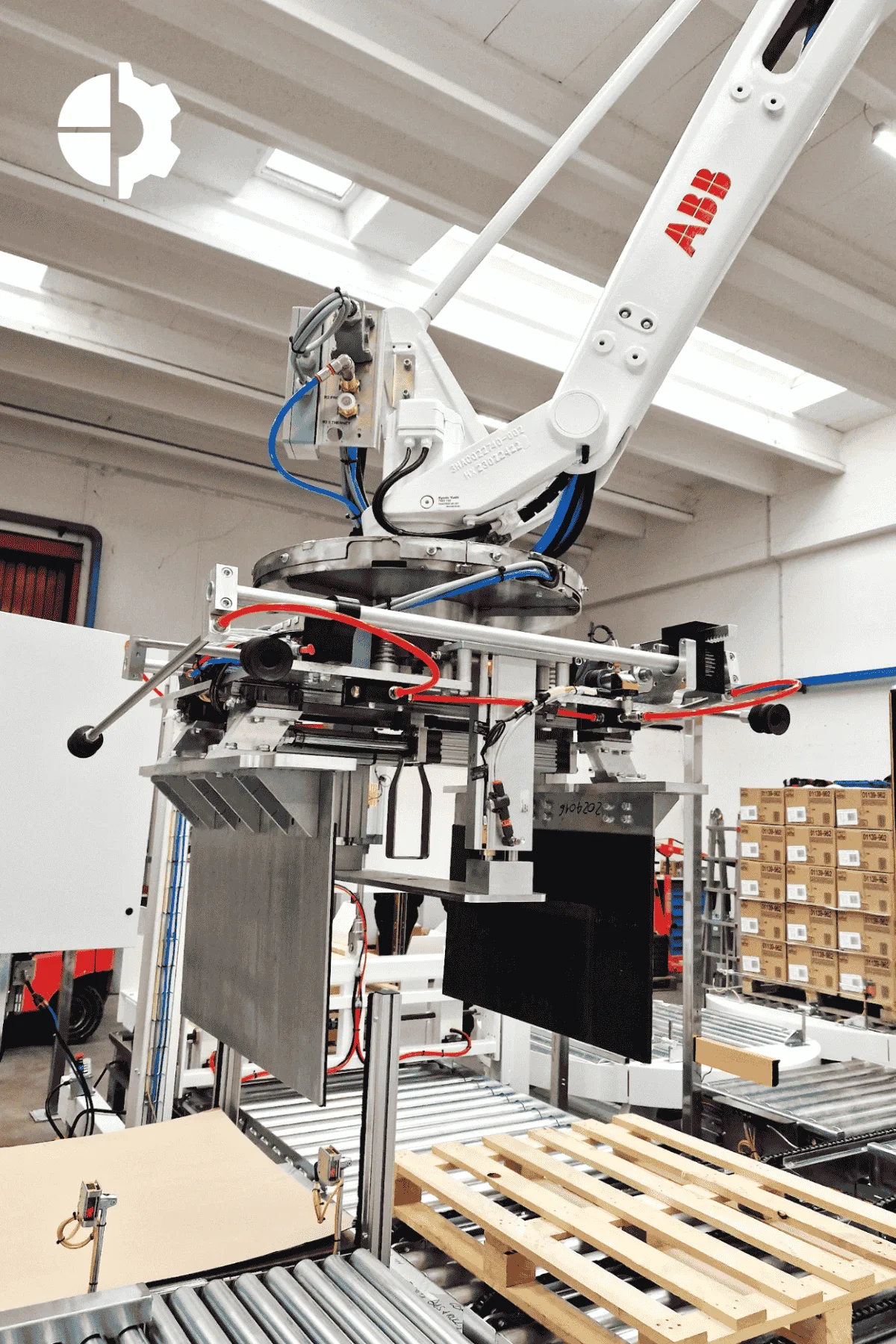
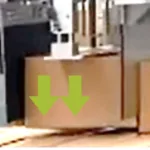
1. Pack moves into position and stops slightly above previous layer
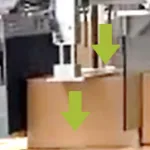
2. Grippers release positive pressure whilst central stabiliser holds the pack down
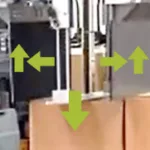
3. Robot retract as the stabiliser continues to hold the pack down
Multiple pack variations
- Bespoke “user-friendly” pallet stacking design software and user interface
- Ability to store and recall over 100 stacking programs as the files are not stored in the PLC
- Increased PLC speed
- Screen showing machine status and pallet positions
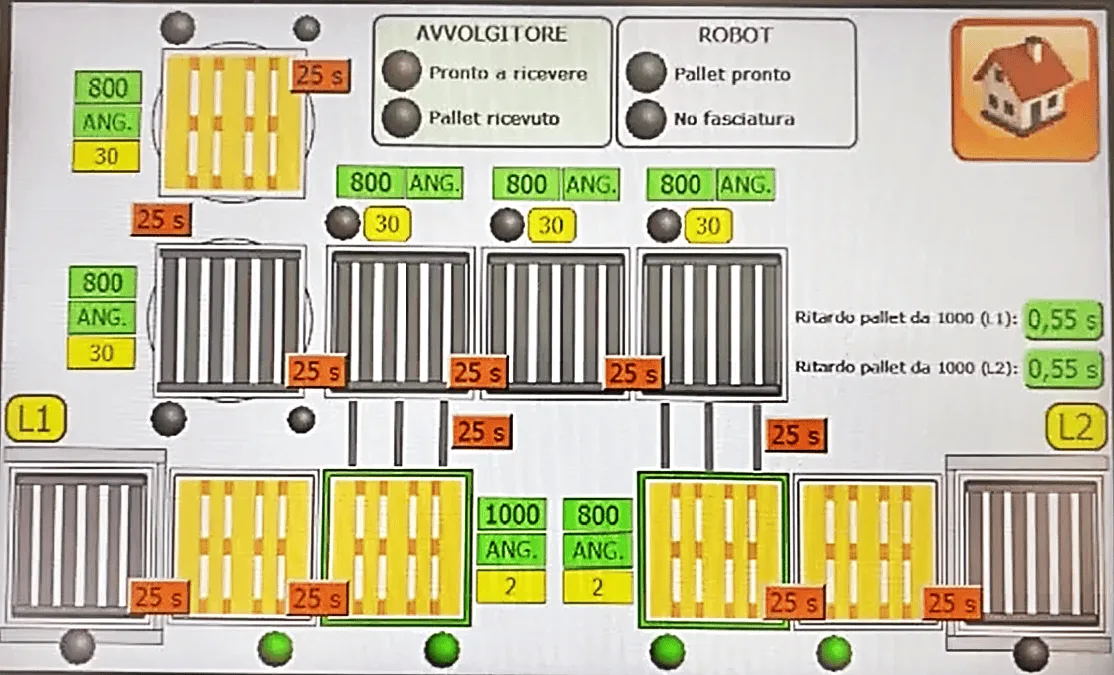
Two pallet sizes
- Compact adjustable pallet de-stacking magazines dispensing each pallet size as required
- Palletiser capable of positioning and stacking both pallet sizes with one robot simultaneously
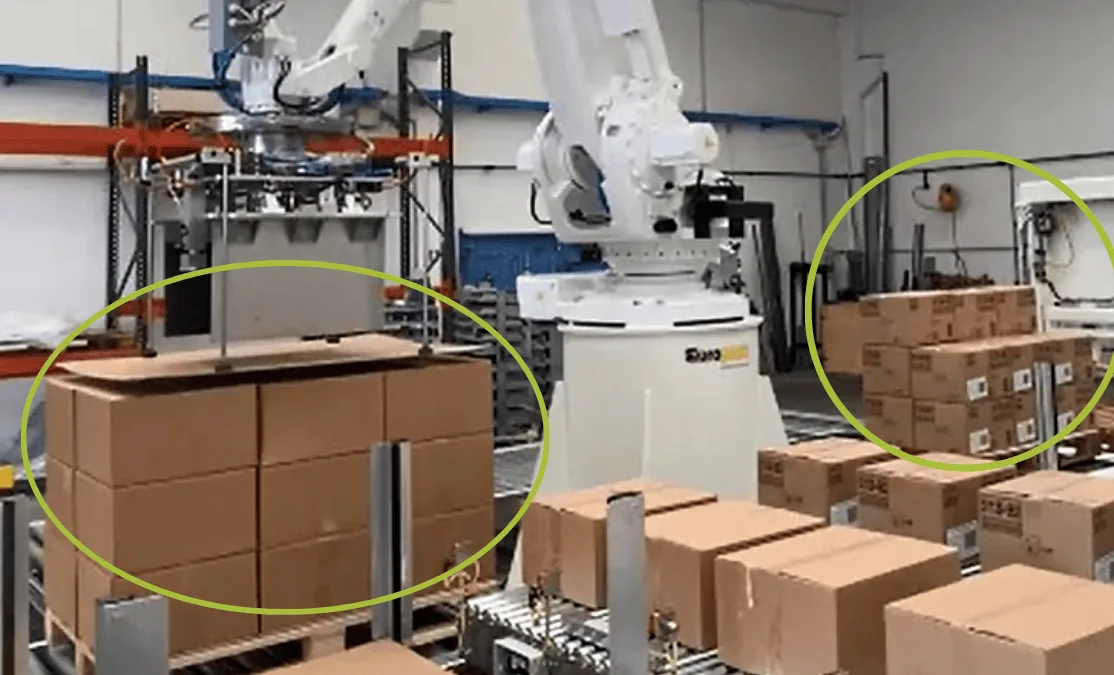
Two different size layer cards
- Adjustable layer card magazines
- Layer card suction cups automatically retract after positioning
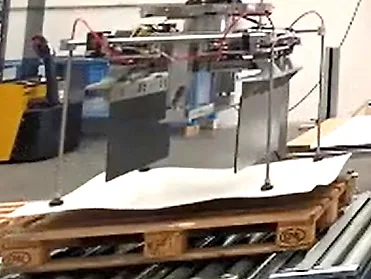
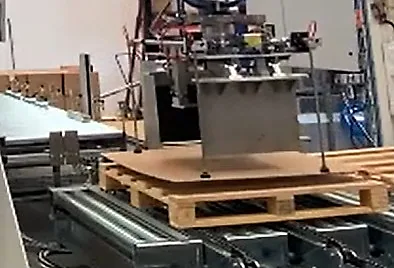
Manual corner post positioning
- Remote panel allows operator to pause the pallet conveyors and safely position 4 x corner posts
- 2 x corner post positioned at a time using a turntable to rotate the pallet by 180 degrees to position 2 x more without fully entering the cell
- Manual light curtain reset to allow conveyors to continue safely after positioning
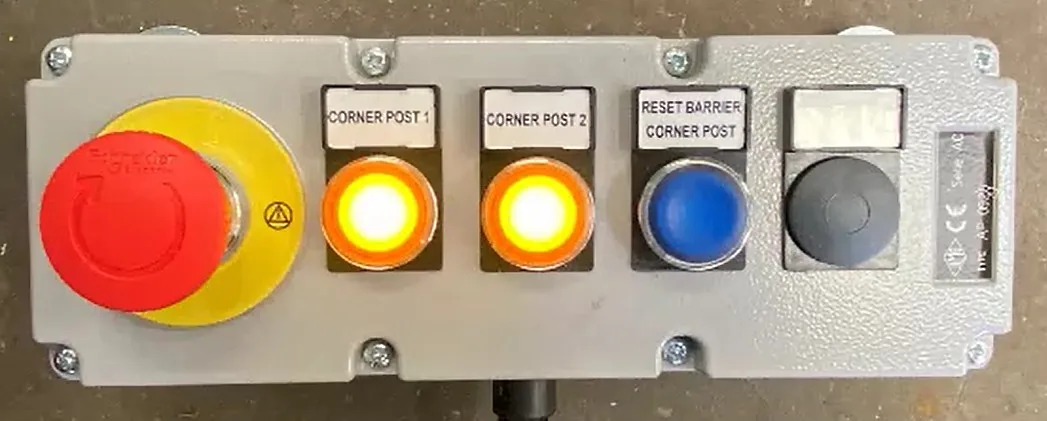